
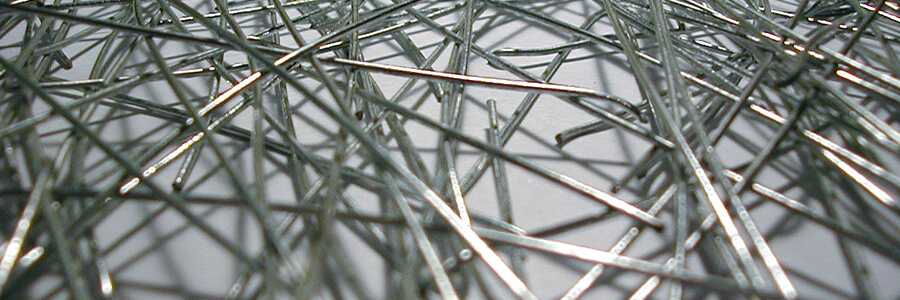
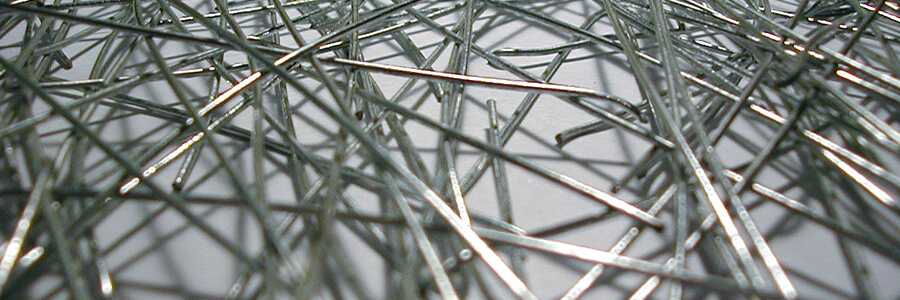
Since the turn of the decade, the leaded vs lead-free solder debate has been ravaging behind the scenes in the electronic manufacturing industry. Which is the right solder to use?
Well in this article we are going to explore this debate. By outlining the benefits of both, their limitations, and our future projections.
Firstly, Let’s Look At The Problem …
In most electronic manufacturing applications, solder fuses components onto printed circuit boards.
The type of solder used by these companies is regulated (more on this below). This means that many soldering processes have switched to lead-free options. The manufacturing process for PCB assembly has become receptive to processes that reduce energy consumption, lower carbon emissions, and are less toxic.
For that reason, leaded solder use is now under the microscope.
Before we go any further though, let's look at both of the wire compositions in a little more detail.
What Are the Two Solder Wires Made From?
Leaded – To get leaded solder wire, you mix both lead and tin alloys together. This provides a lower melting point, aiding in less thermal impact from the soldering process onto your PCB. You can always distinguish a leaded joint by its brighter appearance. This allows you to identify oxidisation far quicker.
Lead-Free – Many manufacturers use lead-free solder to remove lead from their production process. Lead-free solder offers a replacement for the more conventionally used 60/40 SnPb solder wire. Often these versions will have a percentage of the following alloys to replace the lead content: Silver, Copper, Nickel, and Zinc.
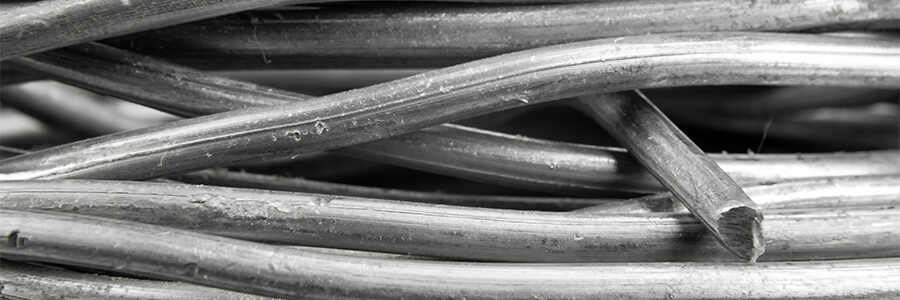
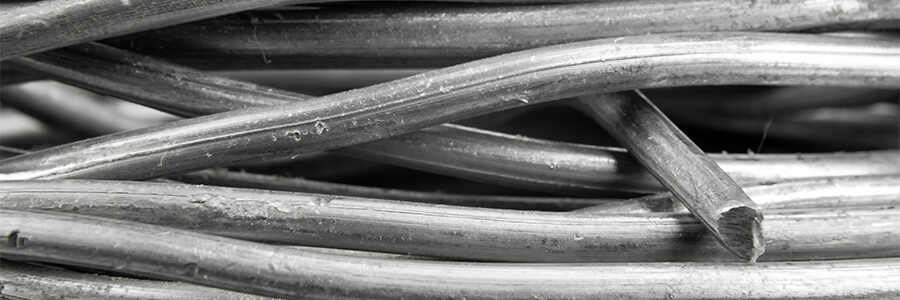
What Is The Problem With Leaded Solder Then?
As a business, unless you operate within the military or medical sector, you must use lead-free solder.
Since 2006 under RoHS guidelines and the Electrical and Electronic Equipment Regulations 2012, restrictions are in place for the use of lead and other hazardous substances.
These restrictions have been born from environmental and sustainability concerns. We explain this in greater detail a little later.
There are more common disadvantages of using leaded solder, which are the following:
- Fumes – As a by-product of the leaded soldering process, it produces hydrogen cyanide and carbon monoxide. These gases are toxic if breathed in. Fume extraction equipment is therefore essential. Although we would argue that this is also the case for any soldering application.
- Poor Heat Dissipation – Overheating your solder joint is a common issue when working with leaded solder. This is because the thermal resistance of this solder wire is much lower. This can often lead to PCBs and other electrical components becoming damaged in the process.
- Higher Fire Risk – Once you expose leaded solder to the air it becomes highly flammable. Consequently, you must take great care at all times where leaded solder is being used.
Many solder manufacturers, including SolderKing and Almit, specialise in RoHS compliant solder wire. However, certain customers still demand lead-containing alloys. This means the manufacturing of leaded solder wire is still being conducted by them.
The production of these wires is mainly for specific industries such as aerospace and automotive. We will explain why this is the case below.
Why Use Leaded Solder Still?
Since the inception of the electronics industry, lead has formed a vital compound in the soldering sphere. When you mix a tin alloy with lead, the compound melts at a far lower temperature than if they were to stand on their own.
This makes a mix of the two alloys superior. As eluded to above, the process of soldering leaded alloys produces toxic fumes.
However, with the right control of LEV control, you can mitigate the risk it poses. For this reason, not everyone has made the move to banish lead from their assembly processes.
We have thus come up with 5 reasons why people were reluctant to move away from leaded solder.
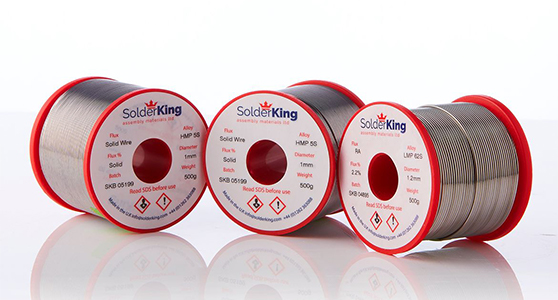
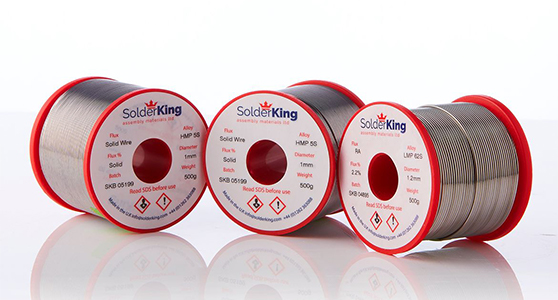
5 Reasons People Still Use Leaded Solder
Melting Temperature
As previously eluded to, the melting point for leaded solder averages around 30°C lower than that of lead-free. This lowers the thermal stress on your components and board.
Your soldering iron also requires less power to heat up to the required temperature. This extends the soldering tip life of your cartridges.
Wetting Capabilities
Leaded solder possesses excellent wetting capabilities. If a solder joint has undertaken a poor wetting process, it can lead to a bad joint.
This is because leaded solder can flow around small holes and narrow spaces far easier. This forms connections far more easily than if you were to have used lead-free solder.
Reworking Projects
Where a product is being reworked, it is essential that the solder and flux chemistries match identically.
This example is never more present than in the aviation sector. Many aircrafts and aircraft systems are soldered with leaded alloys. Because of this, leaded solder needs to be used for any repair work carried out on the system.
To change the solder alloy, the whole system would need to be requalified. These joints however are maintained by industrial personnel, meaning they are never exposed to the general public.
Cost-Effective
At the time of writing, lead is around 1 tenth of the price of tin. This makes the price of lead-free solder wire far more costly.
What’s more, popular solder wire such as SAC305 (Sn96.5Ag3Cu0.5) or SAC405 (Sn95.5Ag4Cu0.5), to name a few, include silver. This alloy is even more expensive than lead, pushing the price you pay for your solder wire even higher.
Tin Whiskers & Tin Pests
Where you are switching to a lead-free solder, you will be using an alloy with a higher percentage of tin content. With this, there are certain draw backs and problems that arise. These are the following:
Tin Whiskers - These are metal filaments that spawn from tin. Their ability to carry current and low electrical resistance make them a threat to the modern electronic circuit. It is widely believed that a tin/lead alloy carries whisker inhibiting abilities once soldered.
Tin Pests - Often referred to as a tin disease. It involves the sudden, and often spontaneous, degradation of tin over time. The tin itself will change from it's silvery metallic state to a brittle and grey form. Over time the alloy will decompose and become powdery, which as you can imagine is not great news for the integrity of your solder joints.
Why Are People Using Lead Free Solder Then?
Now after reading the above, you may think it is crazy to shift away from lead. There are many benefits to using lead alloys in solder wire.
However, the main aim to moving away from a leaded solder is to lessen the waste process and the health hazards posed by soldering. Leaded solder, overall, is more dangerous to work with than lead-free solder formulations.
Complying with these government requirements comes at a cost:
- Your soldering iron will need to operate at a higher temperature.
- You require more flux, meaning your vaporise more flux fumes.
- Fume extraction is still required as lead-free fumes still require extraction.
Therefore, choosing the right tools to work with lead-free solder is imperative.
Solder station manufacturers such as JBC work innovatively to create solutions to this. Improved heat management systems, sleep and hibernation functions to name but a few.
Using lead-free solder is different and took some adjustment.
But the integrity and safety of lead-free solder joints are in no way compromised by the exclusion of lead from your process.
Once you grasp the behaviour and differences in lead-free alloys, you realise that the act of soldering is unchanged.
So, What Further Change Is Likely To Happen?
There is a definite shift over recent years in the leaded vs lead-free solder debate.
Many manufacturers operating heavy duty soldering will likely switch to lead-free solder. That is if they haven’t already.
It is likely that over the coming years and decades, the drafting of new regulations will further limit the use of lead alloys. It has happened with leaded fuel and paint – forecasts and trends only point in one direction.
For now however, the leaded vs lead free solder debate will remain contested among solderers across the globe!
Need advice for the best solder wire or paste for your application? Contact our team today to speak to one of our experts.